Tips
For Using Long Forcing Cone Reamers
When shooting 2¾
inch slugs in a 3 inch chamber many shotguns (not just the Mossberg 930) tend to shave lead off of the slug,
especially when using Brenekes. This
is due to the ¼ inch gap between the end of the 2¾ inch case and the start of
the forcing cone at the end of the 3 inch chamber, which frequently has a lip on
it, in spite of the fact that the SAAMI drawings show no lip. Lengthening the forcing cone
and minimizing the lip will mitigate the lead shaving problem.
CAVEATS!!!!
- The
outside of some shotgun barrels taper down very quickly just forward of the
chamber and the walls would become very thing in a long forcing cone were
cut in them. If you have any
doubts about extending the forcing cone in any barrel, DON'T DO IT.
- Prior
to doing any work check the chamber/forcing cone for chrome plating. This is done by applying cold bluing solution to a clean
area of the chamber. If the
bluing “takes”there is no chrome plating.
If the chamber is chrome plated DO NOT
attempt to use a standard reamer. You will ruin it (the reamer) and they're
pricey. Use a carbide reamer (very pricey) if you need them.
Equipment
- Cutting
oil like Rigid thread cutting oil, Oatey thread cutting oil, 20:1 soluble
oil, or any other thread cutting oil. Available
at Home Depot, hardware, and plumbing supply stores. If necessary you can also use 120W-140W hypoid gear oil.
- 10”,
½” capacity die wrench
- Depending
on the reamer you use (in my case a Clymer #1017 straight flute reamer) you
may find that the shank isn't long enough to run the reamer in enough before
your tap wrench hits the projection on the rear of the barrel hood. I
beat this problem by using a ½ drive x 3/8 inch socket adapter on my tap
wrench.
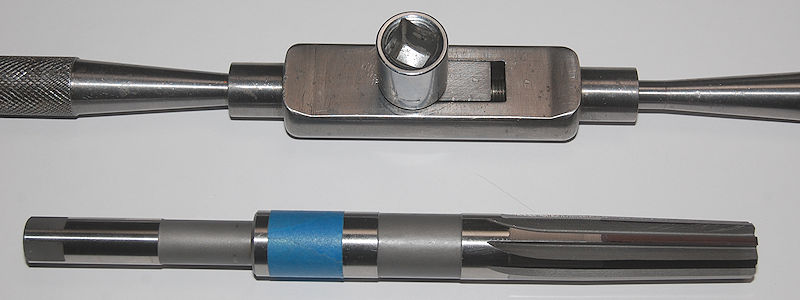 |
Reamer and extension
socket on tap wrench. Note black marks on the reamer (Step 1
below)
Right edge of blue tape wrap denotes the 4.9 inch mark |
Procedure
- Measure
1.9” up from the narrow tip of the reamer and coat each blade with a magic
marker up to the 1.9” mark. I would
also suggest that you measure up 4.9 inches (3 inch chamber), or 4.65 inches
( 2¾ inch chamber) from the tip and put a tape band around the reamer shank
at that point to give you another visual on when you are getting close.
- Position
the barrel horizontally using a padded barrel block in a bench vise, about
waist high, with the muzzle tipped slightly down and the gas port, if
any, up.
- Place
pans under the muzzle and breach to catch any cutting fluid that runs out
during reaming.
- Coat
the reamer and chamber GENEROUSLY
with cutting
oil and carefully insert
the reamer into the chamber.
- Ensure
that the reamer is aligned with the barrel and start turning the reamer in a
clockwise direction while maintaining firm pressure. (Reamer should cut
smoothly.)
- Take
about 4-5 turns with the reamer and carefully withdraw it from the
barrel.
- Carefully clean
ALL chips from the reamer and the barrel
and inspect the barrel. The cut area should be smooth with no traces of
chatter.
- Continue
steps 5 through 8, working slowly and carefully until the black marks you made
on the reamer are all gone and/or the tape band on the shank is close to, or
just barely below the rear of the chamber. If
you go a LITTLE past the end of your marks it's ok but do not
over do it.
- Carefully
clean and inspect the chamber. There should be a smooth transition from the
chamber to the forcing cone, with no, or hardly any apparent step.
Note that if your chamber is close to maximum diameter it may not be
possible to completely remove the step. If a step is visible run the reamer in just a little further until
the step is gone, but no more that .05 past the 4.9 inch or 4.65 inch depth
mark.
For a copy of the
SAAMI 12 ga smooth bore chamber drawings click here.
STOP!
Clean the reamer
carefully and replace it in its container. DO IT NOW!
Then
...
The reamer generally
gives a good finish but some people like to further polish things.
You can use a small 2-stone brake cylinder hone, a “flex-hone” tool
from Brownells, or various grits of wet/dry abrasive paper on a bore brush or
bore mop, starting with 320 grit, and using a variable speed drill.
USE PLENTY OF OIL. If
your initial finish is very smooth you can final polish using KG12 bore polish.
Thoroughly clean the
barrel, assemble your shotgun, and go shoot.
Please email comments or questions to Fr. Frog by
clicking here.
| Back to Fr. Frog's Homepage | Mossberg
930 Page |
Disclaimer
As far as I know all the
information presented above is correct and I have attempted to ensure that it
is. Everything above worked fine for me, but your mileage may vary. I am not
responsible for any errors, omissions, or damages resulting from
the use or misuse of this information, nor for you doing something stupid with
it. (Don't you hate these disclaimers? So do I, but there are people out there
who refuse to be responsible for their own actions and who will sue anybody to
make a buck.)

Updated 2022-10-10 @ 1600